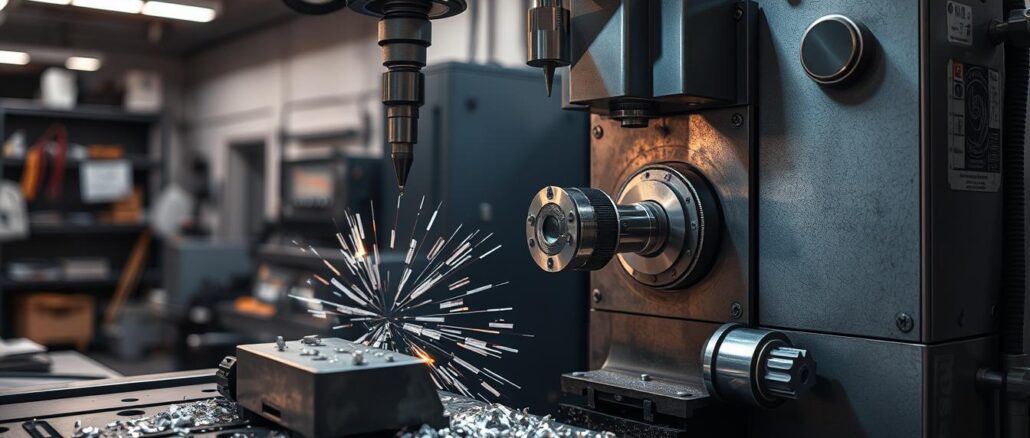
Wussten Sie, dass die optimale Schnittbreite beim Fräsen etwa 2/3 des Durchmessers des Werkzeugs beträgt? Diese überraschende Tatsache verdeutlicht, wie präzise und spezifisch die Fräsbearbeitung sein kann. Das Fräsen zählt zu den wichtigsten spanenden Fertigungsverfahren und wird insbesondere in der metallverarbeitenden Industrie eingesetzt. Dabei wird Material in Form von Spänen abgetragen, was durch die rotierende Bewegung des Werkzeugs ermöglicht wird.
Beim Fräsen rotiert das Werkzeug um seine eigene Längsachse und bearbeitet das Werkstück durch eine Vorschubbewegung. Dieses Verfahren wird nach DIN 8589 in verschiedene Bereiche unterteilt, darunter das CNC-Fräsen, welches eine hohe Maßgenauigkeit und Automatisierung gewährleistet.
Die Vielseitigkeit des Fräsens zeigt sich auch in den verschiedenen Fräsmaschinen und Fräswerkzeugen wie Schaftfräser, Radiusfräser und Fräsköpfe. Die unterschiedlichen Fräsverfahren sind branchenübergreifend von Bedeutung – vom Maschinenbau bis hin zur Luft- und Raumfahrttechnik. In sensiblen Branchen wird beispielsweise das Hochgeschwindigkeitsfräsen (HSC) angewendet, um präzise und schnelle Ergebnisse zu erzielen.
Wichtige Erkenntnisse
- Fräsen ist ein präzises Verfahren, bei dem Material in Spänen abgetragen wird.
- Die optimale Schnittbreite beträgt rund 2/3 des Werkzeugdurchmessers.
- CNC-Fräsen garantiert hohe Maßgenauigkeit und Automatisierung.
- Hochgeschwindigkeitsfräsen ist in der Luft- und Raumfahrt von großer Bedeutung.
- Vielzahl an Fräswerkzeugen und Maschinen ist für spezialisierte Industrieanwendungen verfügbar.
Was ist Fräsen?
Fräsen ist ein zerspanendes Fertigungsverfahren, das in diversen Industriezweigen wie dem Maschinenbau, der Medizintechnik und der Automobilindustrie Verwendung findet. Gemäß DIN 8589 gehört das Fräsen zur Gruppe der spanenden Fertigungsverfahren mit geometrisch bestimmter Schneide. Vor 1840 wurden Formen wie Nuten und Führungen hauptsächlich durch Hobeln hergestellt, doch mit der Entwicklung der Fräsmaschine änderten sich die Herstellungsprozesse grundlegend. Das älteste Fräswerkzeug wird Jacques de Vaucanson aus dem Jahr 1760 zugeschrieben, während die erste bekannte Fräsmaschine 1818 von Eli Whitney gebaut wurde. Diese Maschine diente vor allem zur Herstellung von Schusswaffenteilen.
Die Frästechniken unterscheiden sich erheblich, darunter fallen Schrupp- und Schlichtfräsen sowie Plan- und Rundfräsen. Besonders relevant ist die Herstellung von kreiszylindrischen Flächen beim Rundfräsen, wobei zwischen Innen- und Außenrundfräsen unterschieden wird. Zudem gibt es das Profilfräsen, bei dem ein bestimmtes Werkzeugprofil auf dem Werkstück abgebildet wird. Fräsen wird nicht nur für die Metallbearbeitung genutzt, sondern auch für Kunststoffe und Holz. Ein bedeutender Teil aller Zahnräder wird durch das Verfahren des Wälzfräsens gefertigt.
Fräsen hat die Besonderheit, dass die einzelnen Schneiden des Werkzeugs nicht ständig Kontakt mit dem Werkstück haben. Dabei sind Hartmetallfräser oft die bevorzugte Wahl für hohe Präzision und Langlebigkeit. Die Schnittbreite bestimmt, wie weit die Schneide des Werkzeugs in das Material eingreift – üblicherweise etwa zwei Drittel der Werkzeugbreite. Ein wichtiger Aspekt ist das Gleichlauffräsen, bei dem der Fräser mit maximaler Spanungsdicke in das Werkstück eintaucht und mit minimaler Dicke wieder austritt.
Ein weiterer Vorteil des Fräsens ist, dass es ausschließlich maschinell durchgeführt wird, was eine hohe Automatisierung und Präzision ermöglicht. Moderne CNC-Fräsmaschinen sind in der Lage, komplexe Geometrien und hohe Stückzahlen effizient zu bewältigen. Während das Planfräsen der Herstellung ebener Flächen dient, ermöglicht das Wälzfräsen die präzise Bearbeitung von Zahnrädern und anderen komplexen Formen.
Geschichte des Fräsens
Die Geschichte des Fräsens begann wesentlich in der amerikanischen Waffenfertigung und verbreitete sich dank technischer Innovationen wie Elektromotoren und digitalen Steuerungen. Dieser Fortschritt war ein bedeutender Teil der Geschichte der Produktionstechnik. Die erste dokumentierte Fräsmaschine wurde 1818 von Eli Whitney konstruiert. Whitney’s Entwicklung ermöglichte eine präzise Bearbeitung von Metall und begründete die Basis für die industrialisierte Fertigung.
In den Jahren 1949/50 begann die Entwicklung der NC-Technik durch John Parsons am Massachusetts Institute of Technology in den USA. Die erste NC-gesteuerte Maschine „Cincinnati Hydrotel“ wurde in dieser Zeit konstruiert.
Im Jahr 1954 übernahm die US-Firma Bendix die Technologie von Parsons und entwickelte die erste NC-Maschine mit über 300 Elektronenröhren. Bereits zwei Jahre später waren etwa 100 NC-Maschinen in der US-Luftfahrt im Einsatz. Ende der 50-er Jahre hielt die NC-Technik auch in den Industriestaaten Europas Einzug.
Die Erfindung von Mikroprozessoren in den 1970er Jahren leitete eine neue Ära ein. Eine wesentliche Innovation war die Entwicklung der ersten CNC-Maschine im Jahr 1978. Diese Technologie verbesserte erheblich die Effizienz und Wirtschaftlichkeit in der industrialisierten Fertigung. Bis Mitte der 90er Jahre wurden CNC-Programme mühsam per Hand geschrieben, doch ab der Jahrtausendwende begann man, die Programme direkt aus einem CAD/CAM-System zu erzeugen.
Die Flexibilität und Präzision von CNC-Frästechniken finden heute vor allem in der Metallbearbeitung Anwendung, werden aber auch bei Kunststoff- und Holzverarbeitungen genutzt. Durch die kontinuierliche Weiterentwicklung der CNC-Technologie ist die Frästechnik inzwischen in zahlreichen Industriebereichen nicht mehr wegzudenken. Die CNC-Technik trägt somit weiterhin entscheidend zur Geschichte der Produktionstechnik bei und hat die industrialisierte Fertigung revolutioniert.
Fräswerkzeuge und Schneidstoffe
Fräswerkzeuge sind vielfältig und nutzen geometrisch definierte Schneiden, die es ermöglichen, unterschiedlichste Materialien präzise zu bearbeiten. Hierbei kommen verschiedene Materialien wie Schnellarbeitsstähle und Hartmetalle zum Einsatz. Schnellarbeitsstahl (HSS) bietet eine höhere Zähigkeit und Kantenfestigkeit im Vergleich zu Hartmetall, was ihn besonders vorteilhaft für Anwendungen macht, bei denen Robustheit und Zähigkeit gefragt sind.
Hartmetalle hingegen ermöglichen die Bearbeitung hochfester Edelstähle oder gehärteter Stähle. Diese Werkzeuge erfordern in der Praxis eine Kühlung, um ihre Schneidfähigkeit aufrechtzuerhalten und Kamm- und Querrisse zu verhindern. Ein weiteres wichtiges Material im Bereich der Fräswerkzeuge ist der polykristalline Diamant (PKD), der als Schneidstoff in Zerspanungswerkzeugen eingesetzt wird und die höchste Standzeit bietet.
Im Bereich der CNC-Frästechnik spielen vor allem Hartmetallschneidstoffe eine herausragende Rolle. Diese ermöglichen hinsichtlich Hochgeschwindigkeitsfräsen beeindruckende Leistungen, wobei Fräsmaschinen mit Motorspindel Geschwindigkeiten bis zu 200.000/min erreichen können. Ein Beispiel für spezifische Fräsarbeiten sind Vollfräser aus Hartmetall, die speziell für die Bearbeitung von hochfesten Materialien konzipiert sind.
Die Vielzahl an Fräsertypen umfasst unter anderem Schaftfräser, Walzenfräser, T-Nuten-Fräser, Schlitzfräser und Winkelfräser. Besondere Beachtung finden auch Schrupp- und Schlichtfräser, wobei Schruppfräser ideal für das effektive Entfernen von Material vor dem Feinschliff sind, während Schlichtfräser eine bessere Oberflächengüte bieten. Hinsichtlich der Schneidstoffe dominieren allerdings Hartmetalle und HSS, je nach spezifischen Bearbeitungserfordernissen. Für die Kunststoffverarbeitung finden vor allem einschneidige Fräser Verwendung, welche durch ihre spezifischen Geometrien für präzise Schnitte sorgen.
- Verschiedene Arten von Fräsern, darunter Schaftfräser und Walzenfräser
- Schnellarbeitsstahl (HSS) für höhere Zähigkeit
- Vollfräser aus Hartmetall für hochfeste Materialien
- Polykristalliner Diamant (PKD) für höchste Standzeit
- Hochgeschwindigkeitsfräsen mit bis zu 200.000/min
Arten von Fräsen
Die Arten des Fräsens sind vielfältig und unterscheiden sich je nach Schnitttechnik und Anwendung. Ein gängiges Unterscheidungsmerkmal ist die Laufrichtung. Es gibt das Gleichlauffräsen und das Gegenlauffräsen. Obwohl das Gegenlauffräsen besonders bei der Holzbearbeitung die Kontrolle durch die Hand verbessert, wird aufgrund der besseren Stabilität oft das Gleichlauffräsen bevorzugt, besonders für ungeübte Heimwerker.
Beim manuellen Fräsen gibt es zwei Hauptverfahren: das Freihand-Fräsen und das Vorrichtungs-Fräsen. Freihand-Fräsen ermöglicht eine flexible Bearbeitung, während das Vorrichtungs-Fräsen präzisere Schnitte bietet. Ebenso wichtig sind die unterschiedlichen Fräser-Designs wie Schruppfräser, Scheibennutfräser und Fräser mit Wechselplatten, die jeweils spezielle Anwendungen unterstützen.
Für die industrielle Nutzung und komplexe Aufgaben bietet das Koordinatenfräsen größere Präzision und Flexibilität. Hierbei kommen oft computergesteuerte Maschinen und CAM-Software zum Einsatz, um hochpräzise Werkstücke herzustellen.
Besondere Verfahren wie das Eckfräsen oder Profilfräsen mit Formwerkzeugen sind notwendig, um individuell geformte Bauteile effizient zu produzieren. Diese Technologien sind in der modernen Fertigung unersetzlich, insbesondere wenn es um die Bearbeitung komplexer Geometrien geht. Neben Holz können auch Materialien wie Aluminium, Bronze, Kunststoffe und viele andere mit den richtigen Werkzeugen und Maschinen effizient gefräst werden.
Das CNC-Fräsen hat die Fertigungsindustrie revolutioniert, indem es eine hohe Präzision und Wiederholgenauigkeit ermöglicht. CNC-Fräsmaschinen sind in der Lage, verschiedene Materialien wie Metalle, Kunststoffe und Holz zu bearbeiten und sind in der Regel mit fortschrittlicher CAM-Software ausgestattet, die eine genaue Steuerung und Anpassung der Bearbeitungsparameter ermöglicht.
Abschließend sei gesagt, dass das Kopierfräsen für die Reproduktion von Bauteilen verwendet wird, indem eine Vorlage als Muster dient. Dieses Verfahren ist besonders in der Holzverarbeitung weit verbreitet und erleichtert die Herstellung mehrerer identischer Teile.
Fräsmaschinen
Fräsmaschinen sind ein wichtiger Bestandteil der modernen industriellen Fertigung. Sie reichen von einfachen Universalfräsmaschinen bis hin zu komplexen CNC-gesteuerten Bearbeitungszentren. Diese Geräte zeichnet aus, dass sie mehrere Achsen simultan steuern und dabei eine präzise Bearbeitung gewährleisten können.
Historisch betrachtet geht die Entwicklung der Fräsmaschinen bis ins Jahr 1860 zurück, als Joseph Brown die erste automatische Universalfräsmaschine erfand. Durch die Einführung von CNC-Steuerungen haben sich die Bearbeitungszentren erheblich weiterentwickelt, was nicht nur die Effizienz, sondern auch die Genauigkeit der Fräsprozesse gesteigert hat.
Fräsmaschinen können verschiedene Konstruktionen haben, einschließlich der robusten Portalfräsmaschinen, die sich durch ihre Stabilität und Effizienz bei der Bearbeitung großer Werkstücke auszeichnen. Diese Maschinen sind besonders in der Luftfahrtindustrie und im Formenbau von Bedeutung. Im Gegensatz dazu sind Konsolfräsmaschinen ideal für kleinere und mittelschwere Werkstücke, während Bettfräsmaschinen für schwere und sperrige Teile konzipiert sind.
Eine typische Universal-Werkzeugfräse und Bohrmaschine kombiniert vertikale und horizontale Spindeln und ermöglicht somit vielseitige Anwendungen. Dies macht sie besonders bei Einzelproduktionen und in Werkstätten beliebt.
Die modernen CNC-Fräsmaschinen verwenden hydraulische Werkzeugspannsysteme für schnelle und automatische Werkzeugwechsel, was die Effizienz der Fertigungsprozesse weiter erhöht. Diese Maschinen sind die bevorzugte Wahl für Unternehmen, die höchste Präzision und Produktivität benötigen. Es ist auch wichtig, die richtigen Frästechniken wie Schlichten, Schruppen, Nutfräsen und Konturfräsen je nach Anwendung und Materialwahl einzusetzen.
Zusammenfassend sind Fräsmaschinen nicht nur unerlässlich für die industrielle Fertigung, sondern auch für die Ausbildung und den Prototypenbau, da sie Flexibilität und Vielseitigkeit bieten. Von einfachen Universalfräsmaschinen bis hin zu CNC-gesteuerten Bearbeitungszentren – jede Maschine erfüllt einen spezifischen Bedarf und trägt zur kontinuierlichen Weiterentwicklung moderner Fertigungsprozesse bei.
Verfahrensvarianten beim Fräsen
Das Fräsen zählt zu den mehrschneidigen Zerspanverfahren und bietet verschiedene Variationsmöglichkeiten, darunter das Planfräsen und das Umfangsfräsen. Ein wichtiger Aspekt beim Fräsen ist die unterschiedliche Verfahrensweise bei Gleichlauffräsen und Gegenlauffräsen, bei denen die Vorschubrichtung des Werkstücks und die Schnittgeschwindigkeit entscheidend für die Spanbildung sind.
Beim Gleichlauffräsen bewegt sich das Werkstück in die gleiche Richtung wie die Schneidkante, was zu glatteren Oberflächen führt und den Werkzeugverschleiß minimiert. Im Gegensatz dazu bewegt sich beim Gegenlauffräsen das Werkstück entgegen der Schneidkante, was oft zu einer höheren Belastung des Werkzeugs führt, aber in bestimmten Anwendungen bevorzugt wird.
Eine weitere wichtige Unterkategorie ist das Planfräsen, das hauptsächlich zur Bearbeitung ebener Flächen verwendet wird. Beim Planfräsen erreicht der Eingriffswinkel von 90° die maximale Spandicke, was zu einer effizienten Materialentfernung führt. Die Oberflächengüte beim Fräsen wird stark von der Schneidengeometrie beeinflusst, einschließlich Freiwinkel, Keilwinkel, Spanwinkel, Neigungswinkel und Einstellwinkel. Beispielsweise kann die Oberflächengüte durch Planfasen an den Schneidecken verbessert werden.
- Beim Planfräsen werden ebene Flächen bearbeitet.
- Das Gleichlauffräsen sorgt für glattere Oberflächen.
- Das Gegenlauffräsen ist in anspruchsvollen Anwendungen vorteilhaft.
Ein weiterer entscheidender Punkt ist die richtige Wahl der Schneidstoffe, wie z. B. Schnellarbeitsstähle und zähe Hartmetalle, die zur Verlängerung der Werkzeugstandzeit beitragen. Die Verwendung von Kühlschmiermitteln beim Fräsen mit Hartmetall wird nicht empfohlen, um eine unerwünschte Veränderung der Werkstoffeigenschaften zu vermeiden.
Zusammengefasst sind die Verfahrensvarianten beim Fräsen vielfältig und bieten unterschiedliche Vorteile je nach Anwendung. Sowohl Gleichlauffräsen als auch Gegenlauffräsen haben ihre speziellen Einsatzbereiche, während das Planfräsen zur Erstellung präziser ebener Flächen dient.
Fräsen in verschiedenen Industrien
Das Fräsen ist in zahlreichen Branchen wie dem Maschinenbau, der Elektrotechnik und der Raumfahrt ein unverzichtbares Fertigungsverfahren. Insbesondere in der Automobilindustrie spielt das Fräsen eine zentrale Rolle. Es ermöglicht die präzise Herstellung von Motorblöcken, Zylinderköpfen und anderen komplexen Komponenten, die für den reibungslosen Betrieb eines Fahrzeugs unerlässlich sind.
Auch in der Luftfahrttechnik findet das Fräsen breite Anwendung. Passgenaue Teile wie Flugzeugrippen, Strukturbauteile und Turbinenblätter werden mittels hochentwickelter Fräsverfahren hergestellt. Dies gewährleistet die hohe Qualität und Sicherheit, die in der Luftfahrttechnik unerlässlich sind.
Die Medizintechnik setzt ebenfalls stark auf das Fräsen. Bei der Herstellung von Implantaten, chirurgischen Instrumenten und Prothesen ist eine hohe Präzision erforderlich. Das Fräsen ermöglicht die exakte Anpassung dieser Geräte an die individuellen Bedürfnisse der Patienten, was zu besseren Behandlungsergebnissen beiträgt.
Vorteile und Nachteile des Fräsens
Fräsen ist eine der wichtigsten Werkzeugmaschinen für die Fertigungsindustrie nach der Bohrmaschine und der Drehmaschine. Es ermöglicht die Herstellung von Einzelteilen in kleinen oder großen Serien und die Abtragsleistung bei Fräsmaschinen ist schneller als bei Drehmaschinen. Besonders das CNC Metallfräsen bietet eine höhere Produktionsgeschwindigkeit und Präzision, was zu niedrigeren Herstellungskosten führt.
Zu den Vorteilen des Fräsens gehört die hohe Präzision und die Fertigungseffizienz. Durch die Verwendung unterschiedlicher Werkzeuge können komplizierte Formen leicht hergestellt werden. Durch CNC-Frästechnologie, die das Austauschen von bis zu 30 verschiedenen Werkzeugen ermöglicht, wird die Fertigungseffizienz weiter gesteigert und die Kosten optimiert.
Jedoch gibt es auch Nachteile. Die Anschaffungskosten für CNC-Fräsmaschinen sind hoch, was besonders bei hochkomplexen Systemen ins Gewicht fällt. Dazu kommt der erhöhte Wartungsaufwand und der Bedarf an qualifiziertem Wartungspersonal. Der Betrieb und die Instandhaltung dieser Maschinen erfordern spezialisierte Fähigkeiten, um einen reibungslosen Betrieb sicherzustellen und minderwertige Produkte durch unzureichende Programmierung und Überwachung zu vermeiden.
Zusammenfassend bietet das Fräsen, insbesondere das CNC-Fräsen, zahlreiche Vorteile durch erhöhte Fertigungseffizienz und Präzision. Gleichzeitig müssen jedoch die hohen Anschaffungskosten und der Wartungsaufwand berücksichtigt werden, um das volle Potenzial dieser Technologie auszuschöpfen.
Umweltaspekte beim Fräsen
In der modernen CNC-Fertigung sind Umweltaspekte von entscheidender Bedeutung. CNC TECHNIC setzt auf energieeffiziente CNC-Fräsmaschinen, um den Energieverbrauch während der Herstellungsprozesse zu minimieren. Diese nachhaltige Produktion hilft nicht nur beim Schutz der Umwelt, sondern spart auch Betriebskosten. Durch die präzisen Frästechniken wird der Materialverbrauch optimiert, was zu erheblicher Ressourceneffizienz führt.
Die Auswahl umweltfreundlicher und recycelbarer Materialien ist ein weiterer wichtiger Bestandteil des Umweltmanagements in der CNC-Bearbeitung. CNC TECHNIC fördert die Verwendung von recycelbaren Materialien in allen Produktionsphasen, welches die Materialverschwendung reduziert und zur Schonung der Ressourcen beiträgt. Dies ist ein wesentlicher Schritt in Richtung einer nachhaltigen Produktion.
Ein weiterer bemerkenswerter Aspekt ist das effektive Schrottmanagement. Die sorgfältige Planung und Programmierung der CNC-Maschinen hilft dabei, das Restmaterial zu minimieren und unnötigen Abfall zu vermeiden. Materialreste können recycelt oder wiederverwendet werden, wodurch der ökologische Fußabdruck des Unternehmens weiter reduziert wird. Lean Manufacturing-Prinzipien und fortschrittliche CAD/CAM-Software tragen dazu bei, den Materialverbrauch zu optimieren und die Umweltbelastung zu senken, was die Position von CNC TECHNIC als Vorreiter im Umweltmanagement in der Fertigungsindustrie stärkt.
Diese integrative Herangehensweise zeigt, dass nachhaltige Praktiken nicht nur umweltfreundlich sind, sondern auch wirtschaftlich sinnvoll. Unternehmen, die auf Ressourceneffizienz und Abfallreduzierung setzen, erzielen nicht nur Kosteneinsparungen, sondern stärken auch ihre Marktposition in einer zunehmend umweltbewussten Geschäftswelt.